Hochgeschwindigkeits-Schneidemaschine Solution
Overview
- Overview
- Features and Benefits
- Related Products
- Related Cases
- Related News & Events
- Related Solutions
- Contact us
Hochgeschwindigkeits-Schneidemaschine Solution
Da die moderne Industrie allmählich in Richtung Industrie 4.0-Ära schreitet, werden auch die Leistungsanforderungen an Automatisierungsgeräte immer höher. Aufgrund einiger seiner Nachteile kann das herkömmliche AC-Servosystem die Anforderungen der Kunden allmählich nicht mehr erfüllen. Um die verschiedenen Nachteile des herkömmlichen Impulsservos zu überwinden, entwickeln viele Servohersteller auf dem Markt aktiv Feldbus-Servoantriebe. Derzeit gibt es Dutzende ausgereifter Feldbustechnologien auf dem Markt. Unter ihnen wird der EtherCAT-Feldbus von den meisten Servoherstellern der Welt aufgrund seiner hervorragenden Leistung und seines offenen Kommunikationsprotokolls bevorzugt. In diesem Artikel wird der Entwicklungsstand der EtherCAT-Feldbustechnologie und die Anwendungserfahrung im tatsächlichen Bereich anhand der „EtherCAT-Feldbustechnologie im Anwendungsfall eines Hochgeschwindigkeits-Bandschneiders“ veranschaulicht.
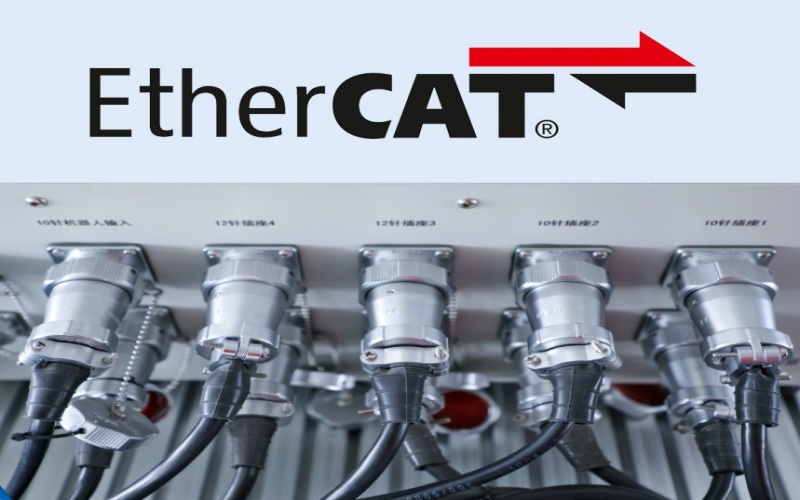
Features and Benefits
Einführung in EtherCAT und seinen Entwicklungsstatus
1. Die Vorteile des EtherCAT-Feldbusses
Schnelle Kommunikationsgeschwindigkeit: Im Vergleich zu anderen Feldbussen verwendet der EtherCAT-Feldbus die Ethernet-Übertragungstechnologie, die die Datenübertragungsgeschwindigkeit erheblich verbessert und eine Kommunikationsgeschwindigkeit von 100 Mbit/s erreicht. Darüber hinaus wird der Vollduplex-Übertragungsmodus verwendet und die Datenübertragungseffizienz weiter verbessert.
Es gibt viele Arten unterstützter Topologien: Der EtherCAT-Bus unterstützt fast alle Bustopologien wie Stern, Bus und Baum. Es bietet mehr Flexibilität beim Routing und unterstützt die automatische Adresszuweisung ohne Festlegen einer IP-Adresse.
Distributed-Clock-Funktion: Die Distributed-Clock-Funktion reduziert den Synchronisierungszeitfehler zwischen zwei Servoachsen auf weniger als eine Mikrosekunde, was bei der Synchronisierungssteuerung der Servoachsen eine entscheidende Rolle spielt.
Hohe Sicherheit: Dank der Verwendung der TwinSAFE-Sicherheitstechnologie ist es nun möglich, das EtherCAT-Sicherheitsprotokoll zu verwenden, um sicherheitsrelevante Kommunikation und Steuerungskommunikation im selben Netzwerk durchzuführen. Dadurch kann der EtherCAT-Bus sicher integriert werden (SIL)3 und kann nach Ergreifen entsprechender Maßnahmen sogar SIL4 erreichen.
2. Entwicklungsstatus des EtherCAT-Feldbusses
Seit seiner Einführung ist der EtherCAT-Feldbus weltweit weit verbreitet. Ende letzten Jahres führte Beckhoff außerdem die EtherCAT-Feldbustechnologie der zweiten Generation ein – EtherCAT G. EtherCAT G nutzt die Gigabit-Ethernet-Kommunikationstechnologie, um die EtherCAT-Leistung auf ein völlig neues Niveau zu bringen. EtherCAT G ist nicht nur vollständig kompatibel mit der vorherigen Generation der 100-Mbit/s-EtherCAT-Technologie, sondern ermöglicht Kunden auch eine zuverlässige Kommunikation ohne Änderung der Parameter der Masterstation und ist ebenso einfach zu verwenden. Darüber hinaus ermöglicht der Branch-Controller-Modus von EtherCAT G den effizienten parallelen Betrieb mehrerer Subnetzsegmente. Als Beckhoff den EtherCAT G Gigabit EtherCAT vorstellte, schlug es auch das Designkonzept des 10 Gigabit EtherCAT 10G vor. Der 10 Gigabit EtherCAT 10G hat eine höhere Kommunikationsrate (100 Gbit/s) und unterstützt somit datenintensive Anwendungen mit hoher Dichte.
3. Anwendung des EtherCAT-Feldbusses auf einer superschnellen Bandschneidemaschine
1) Der Herstellungsprozess von Bändern
Dichtungsbänder sind nicht nur ein wesentlicher täglicher Bedarf in unserem täglichen Leben, sondern haben auch eine breite Palette von Anwendungen in der industriellen Produktion, insbesondere in der Logistik, Verpackung und anderen Branchen. Die Herstellung von Bändern durchläuft vom Rohmaterial bis zum fertigen Band Dutzende komplizierter Prozesse, und zwar wie folgt:
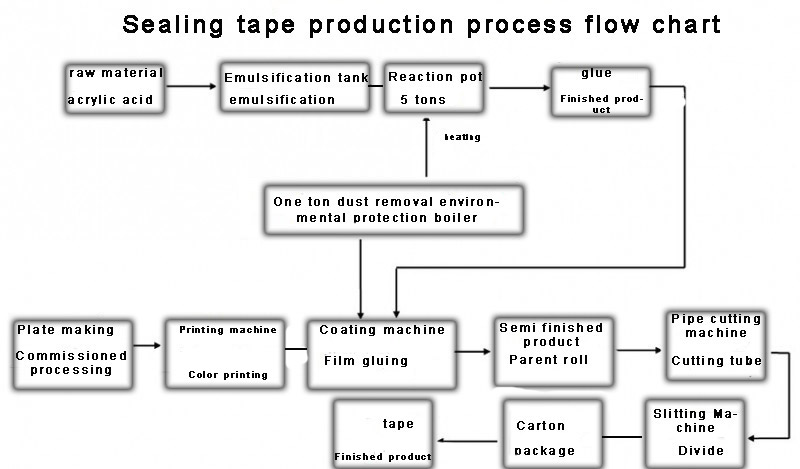
Die Herstellung von Bändern durchläuft vom Rohmaterial bis zum fertigen Band Dutzende komplizierter Prozesse
1. Hinzufügen von Rohstoffen: Als Erstes werden im Bandherstellungsprozess Bandrohstoffe wie Acryl hinzugefügt.
2. Emulgierbehälter: Anschließend wird der Rohstoff für das Klebeband aus Acrylsäure zum Emulgieren in den Emulgierbehälter gegeben.
3. Reaktionsgefäß: Zum Emulgieren wird Acrylsäure in den Emulgierbehälter gegeben und dann zum Erhitzen in das Reaktionsgefäß gegeben.
4. Klebstoff: Nach den oben beschriebenen Prozessschritten zur Bandherstellung wird das fertige Klebstoffprodukt hergestellt.
5. Beschichtungsmaschine: Der soeben hergestellte Klebstoff wird zum Kalibrieren auf eine Folie aufgebracht.
6. Halbfertigprodukte: Durch diese Bandherstellungsprozesse hergestellte halbfertige Bänder – die Mutterrolle.
7. Rohrschneidemaschine: Die soeben hergestellte Bandmutterrolle wird mit einem Rohrschneider geschnitten.
8. Schneidemaschine: Nach dem erfolgreichen Schneiden der Bandmutterrolle wird die Schneidemaschine verwendet, um den Streifenproduktionsprozess durchzuführen.
9. Karton: Nachdem das Band geschnitten wurde, wird es zu der Bandrolle, die wir normalerweise verwenden. Die Bandrolle muss auch verpackt und verpackt werden, und dann wird es zu dem Band, das wir normalerweise verwenden.
10. Band: Legen Sie das verpackte Band in das Lager. Dies ist der letzte Bandproduktionsprozess. Zu diesem Zeitpunkt kann es als fertiges Band bezeichnet werden.
Die Schneidemaschine ist hauptsächlich der letzte Prozess zum Abschluss des Bandproduktionsprozesses. Die traditionelle Lösung des Kunden besteht darin, den Frequenzumsetzer und den gewöhnlichen Impulsservo zu verwenden, um die Spannungsregelung und Etikettierung im Bandstreifenprozess abzuschließen. Das traditionelle Schema hat die Nachteile einer geringen Effizienz und mangelnden Präzision und erzeugt während des Auf- und Abwickelvorgangs des Bandes eine große Menge statischer Elektrizität, die leicht den Empfangsimpuls des Servotreibers stört und dadurch die Produktausbeute verringert.
Als Reaktion auf die Mängel der alten Lösung des Kunden entwickelte das Anwendungsentwicklungsteam von VEICHI durch Diskussion und Analyse eine neue Lösung für eine automatische Schneidemaschine. Durch die Zusammenarbeit des professionellen Spannungsfrequenzumrichters VEICHI AC310 und des Servos vom Typ SD700 EtherCAT-Bus löst es die Probleme der geringen Effizienz und mangelnden Entstörung des alten Schemas.
2) Hardwaredesign des Hochgeschwindigkeits-Schneidgeräts
Der letzte Schritt im Bandproduktionsprozess besteht darin, das produzierte Masterrollenband mithilfe des Schneidgeräts in fertige Bänder zu teilen. Das in diesem Fall entwickelte Hochgeschwindigkeits-Schneidgerät ist das Automatisierungsgerät, um diesen Schritt abzuschließen. Das gesamte Steuerungssystem kann grob in drei Teile unterteilt werden, die separat gestaltet werden können, nämlich: 1. Teil der synchronen Interpolationsbewegung des Roboters, 2. Teil der Spannungsregelung des Wechselrichters, 3. Teil der Etikettierbewegung.
(1)Teil der synchronen Interpolationsbewegung des Roboters:
Um das Problem der geringen Effizienz des alten Systems zu lösen, haben wir im neuen System einen Roboter zur Be- und Entladeaktion hinzugefügt, was die Produktionseffizienz um fast 50 % erhöht hat.
Der Manipulatorteil besteht aus zwei Gelenkmanipulatoren. Die vier Servos vom Typ VEICHI SD700 EtherCAT-Bus werden verwendet, um die Gelenkbewegung der Maschine anzutreiben. Die Schwierigkeit dieses Teils der Steuerung besteht darin, dass die Synchronisierung der linken und rechten Manipulatoren während der Bewegung sichergestellt werden muss. Der Fehler darf 2 Mikrosekunden nicht überschreiten, und die Bewegung der beiden Gelenke eines einzelnen Roboters muss auch den Interpolationsalgorithmus beinhalten. Daher ist es sehr schwierig, die Synchronisierung zwischen den beiden Achsen sicherzustellen und gleichzeitig die Interpolationsbahn sicherzustellen. Der VEICHI SD700 EtherCAT-Bus-Servoantrieb verwendet das Prinzip der verteilten Taktsynchronisierung zur Steuerung der Positionsschleife. Die Zeitsynchronisierungsperiode beträgt nur 125 Mikrosekunden und der Positionssynchronisierungsfehler zwischen den beiden Achsen beträgt etwa 1 Mikrosekunde, sodass die Leistung die Prozessanforderungen vollständig erfüllen kann.
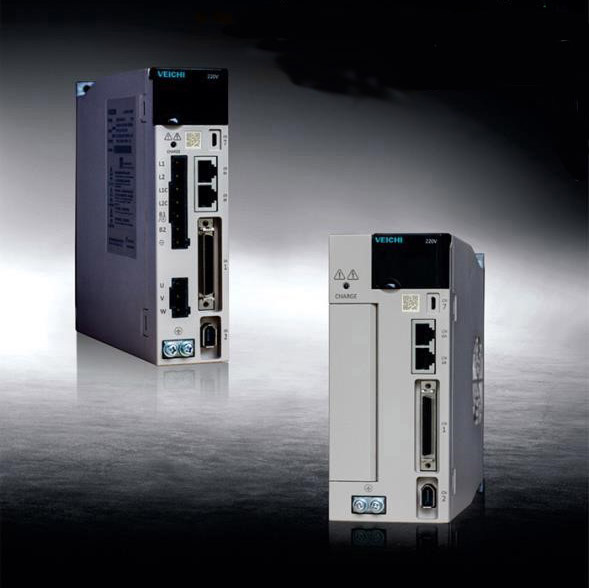
VEICHI-Servoantrieb
(2) Spannungsregelungsabschnitt des Wechselrichters
Das alte Schema verwendet einen gewöhnlichen Frequenzumsetzer. Da die Maschine während des Betriebs des Längsschneiders ständig starten und stoppen muss, kommt es in der Start-Stopp-Phase häufig zu Spannungsschwankungen. Daher hat das System strenge Anforderungen an die Spannungsregelung und die Spannung des gewöhnlichen Wechselrichters. Die Genauigkeit der Regelung ist zu schlecht. Im neuen Schema verwenden wir den neuesten speziellen Spannungsfrequenzumsetzer AC310 von VEICHI, um die Spannungsregelung des Systems zu vervollständigen. Der spezielle Spannungsregelungsfrequenzumsetzer VEICHI AC310 ist speziell für die strenge Spannungsregelung konzipiert. Selbst bei häufigen Start- und Stoppstellen kann die Präzision der Spannungsregelung innerhalb eines Schwankungsbereichs von 1,5 % garantiert werden, und die Spannungsverjüngung ist ebenfalls vorhanden. Durch die Kontrolle werden die verarbeiteten Produkte perfekter.
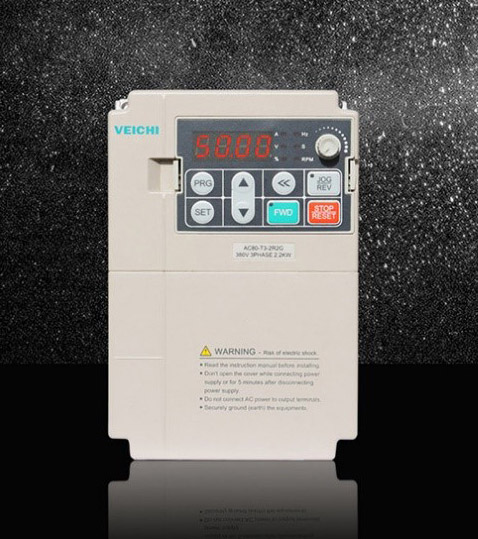
Inverter-Spannungskontrollabschnitt
(3)Etikettierbewegungsteil
Der Etikettierteil des Systems erfordert eine EtherCAT-Taktsynchronisierung. Der Servoantrieb vom Typ VEICHI SD700 EtherCAT-Bus verwendet einen verteilten Taktsynchronisierungsalgorithmus, um die Slave-Achse besser verfolgbar zu machen. Während des Etikettiervorgangs kann es perfekt auf die Spindel abgestimmt werden, den Etikettiervorgang abschließen und die Etikettiergenauigkeit hat im Test 0,1 mm oder weniger erreicht.
(4)Einführung in den Algorithmus zur Roboterpositionssteuerung
Der kompliziertere Teil des gesamten Systems ist der Roboterteil. Da das Design des Manipulatorteils nicht dem traditionellen XYZ-Rechteckkoordinatenmanipulatordesign, sondern dem Doppelgelenkmanipulatordesign entspricht, müssen die Koordinaten der Endposition des Manipulators durch den Vorwärts- und Rückwärtslösungsalgorithmus bestimmt werden. Da das gesamte Systemprogramm zu groß ist, teile ich hier nur den positiven Lösungsalgorithmus des unteren Gelenkroboters und wie man den Roboter steuert, um ihn mithilfe einer Interpolationsbewegung an die angegebene Position zu bringen.
Bestimmen Sie die Beziehung von (X, Y) durch (θ, α):
Durch:
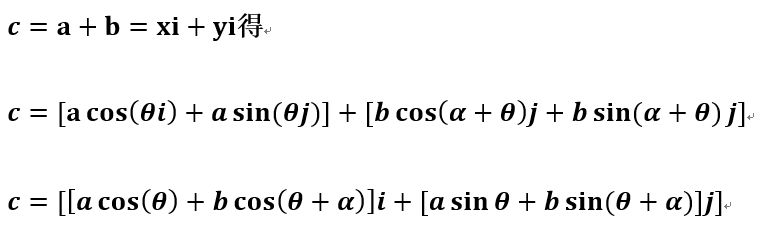
Formel eins
Gereinigt durch die obige Formel:
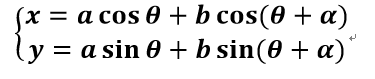
Formel zwei
Nachfolgend sind einige der algoritHMIschen Verfahren zur Robotersteuerung aufgeführt:
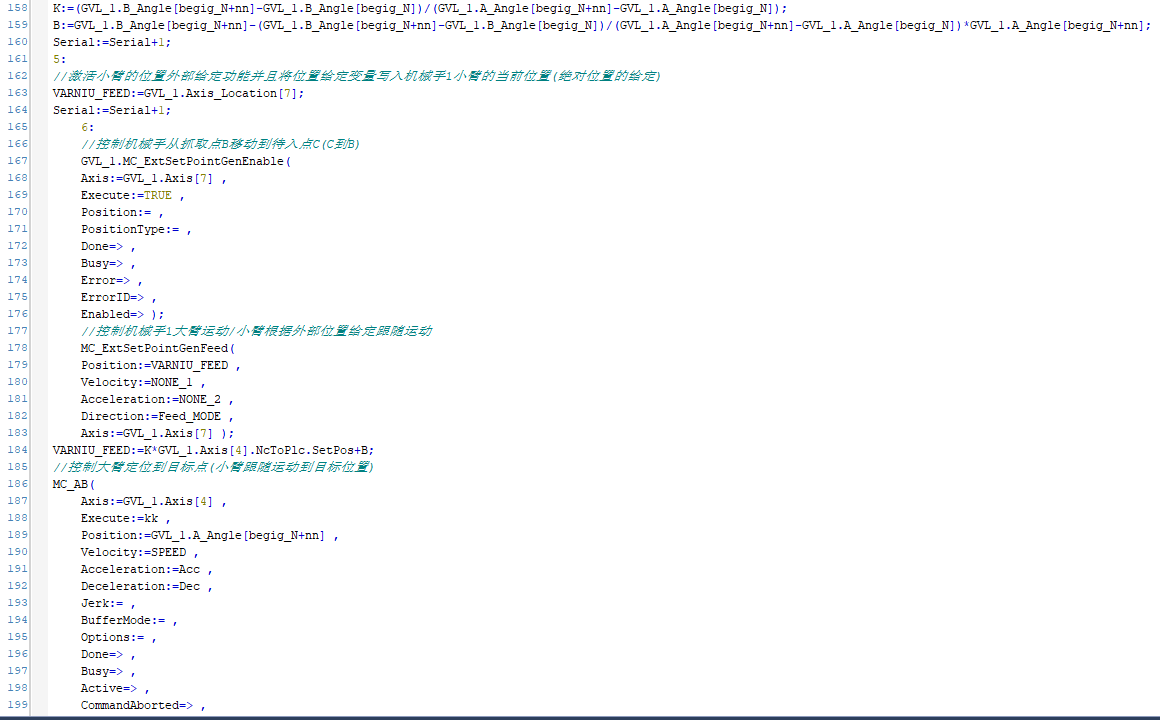
Einige der algorithmischen HMI-Verfahren zur Robotersteuerung
Livefoto
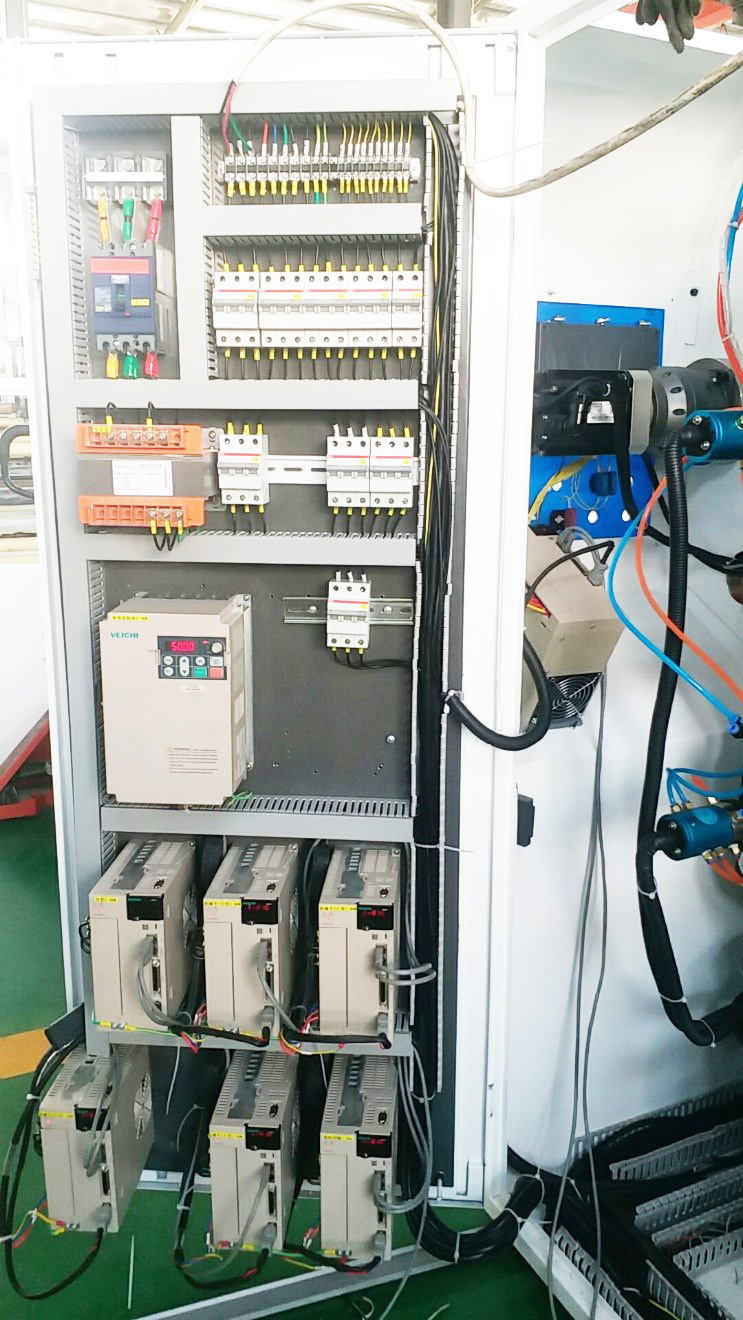
Livefoto
Fazit
Durch die Umstellung auf VEICHI-Bus-Servo- und Spannungsregelungs-Wechselrichter wurde die Leistung der Kundenausrüstung erheblich verbessert. Sowohl die Produktionseffizienz als auch die Genauigkeit der Ausrüstung sind branchenweit führend.
VEICHI hat sich der Entwicklung vorteilhafterer Bus-Servoantriebe verschrieben. Es wurde eine Vielzahl leistungsstarker Bus-Servoantriebe, darunter CANopen, EtherCAT, M-II, M-III usw., erfolgreich entwickelt und auf dem Markt verfügbar gemacht. In zahlreichen Anwendungen haben die Bus-Servoantriebe von VEICHI nach praktischen Tests ein neues Niveau in Bezug auf Leistung und Stabilität erreicht.